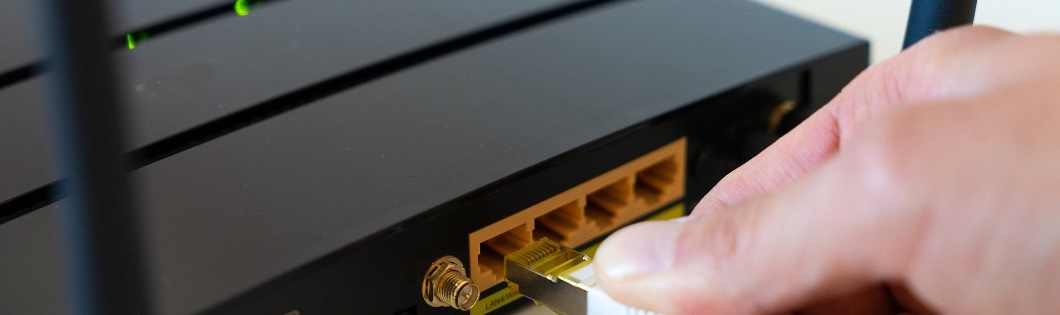
Below are the nine most common plastics for electronic enclosures:
- Acrylonitrile Butadiene Styrene (ABS)
- Acrylonitrile Styrene Acrylester and Polycarbonate (ASA+PC Blend)
- Polyamide (PA)
- Polybutylene Terephthalate (PBT)
- Polycarbonate (PC)
- Polycarbonate + Acrylonitrile Butadiene Styrene (PC+ABS Blend)
- Polymethyl Methacrylate, Acrylic, Plexiglas (PMMA)
- Polyphenylene Ether+Polystyrene (PPE+PS)
- Styrene Ethylene Butadiene Styrene (SEBS)
A more detailed description of these common plastics for electronic enclosures follows, including their uses, attributes, and considerations.
1. Acrylonitrile Butadiene Styrene (ABS)
ABS is one of the toughest thermoplastic polymers. ABS plastic sheeting is a low-cost investment that provides a durable solution for heavy-duty needs.
The automotive and refrigeration industries use ABS, and you can also find it in boxes, toys, luggage, and gauges.
Attributes
- Flexible
- Glossy
- Polyamide (PA)
- Highly processable
- Ideal for enclosed rooms
- Provides extreme resistance against impact
- Provides electrical resistance
- Provides resistance against many chemicals
- Can be used at temperatures down to -4°F
- Has a glass transition temperature of 105°F and a melting point of 392°F
- Flame resistant to UL 94 HB
- Easily custom colorable
- Ranges in thickness from 200 microns to 5mm with a maximum 1600mm width
- No known carcinogenic or other negative health effects
Considerations
- Not ideal for outdoor electronic enclosures
- Doesn’t have UV resistance, so cannot withstand exposure to sunlight
- Loses strength with thin wall thicknesses
2. Acrylonitrile Styrene Acrylester and Polycarbonate (ASA+PC Blend)
Combining Acrylonitrile Styrene Acrylester (ASA) with the thermoplastic Polycarbonate (PC) allows it to withstand various stresses and high temperatures.
Unpainted automotive parts and injection molding often uses this blend. It also has flame-retardant applications.
Attributes
- Provides excellent performance at both high and low temperatures
- Provides increased impact strength
- Provides good chemical resistance
- Resistance to UV and moisture
- Provides waterproof electronics enclosures with excellent moisture resistance
- Flame-resistant to UL 94 V-0, which is the highest resistance level (self-extinguishing within 5-10 seconds)
3. Polyamide (PA)
Polyamides occur naturally in the proteins of wool and silk. Cable ties and power tool housings often use artificially-made polyamide plastics.
Attributes
- Tough and wear-resistant
- Slides well
- Great electrical insulator
Considerations
- Absorbs moisture and is not waterproof, so not ideal for humidity or if needing waterproof electronics enclosures
- Affected by alcohols and acids
4. Polybutylene Terephthalate (PBT)
Plastic electrical enclosures with high-temperature applications often use PBT.
PBT is a thermoplastic polyester, commonly used in electrical engineering housings, automotive construction, and plug connectors.
Attributes
- Resistant to chemicals
- Resistant to stress
- Excellent for high-temperature situations
Considerations
- Crystalline
- Shrink rate doesn’t allow the designer to switch easily to materials like PC or ABS
5. Polycarbonate (PC)
Polycarbonate is in the polyester family and is a highly popular thermoplastic because of its strength and flexibility for applications where metal is not appropriate.
Polycarbonate exists in products ranging from eyewear and bullet-proof glass to medical devices. It is also common in pipes that transport internal LED light to the outside.
Attributes
- Transparent
- Easily colorable
- Extraordinary impact strength
- High ultimate tensile strength and yield tensile strengths
- Polycarbonate sheets are 30 times stronger than acrylic and 250 times stronger than glass.
- Appropriate as plastics for outdoor use
- UV-resistant
- Withstands temperatures from -4°F to 284°F
- Can be cut or cold-formed on site
- Lightweight
- Requires less structural support than glass
Considerations
- Better when combined into ASA+PC-FR if permanent plastics for outdoor use are needed
- Not recommended to use with strong alkalis
- Oil- or alcohol-based chemicals can damage it.
- PC contains BPA, which is not appropriate for all applications.
6. Polycarbonate + Acrylonitrile Butadiene Styrene (PC+ABS Blend)
Polycarbonate and Acrylonitrile Butadiene Styrene are some of the most commonly used plastics for electronic enclosures. A PC+ABS thermoplastic blend combines the positive qualities of both PC and ABS.
The automotive, electronics, and telecommunications industries widely use PC+ABS blends.
Attributes
- Has a very high impact strength
- Can withstand sub-zero temperatures
- Great chemical resistance
- Has the highest flame-resistance level of UL 94 V-0
Considerations
- Best for indoor or limited outdoor plastic electrical enclosures
- Endures moderate corrosive conditions
7. Polymethyl Methacrylate, Acrylic, Plexiglas (PMMA)
Polymethyl Methacrylate is also known as acrylic, plexiglass, or acrylic glass and by several trade names.
Acrylic is often used in electronic enclosures when the designer wants clear thermoplastic material without using polycarbonate. Because PMMA is infrared transparent, it’s also perfect for optical and remote-control applications.
Attributes
- Transparent
- Lightweight
- Shatter-resistant
- Seventeen times more impact-resistant than glass and easier to handle and process
- 392°F boiling point
- Acrylic sheets come in a variety of grades, colors, tints, sizes, and thicknesses
- Varieties with fluorescence, abrasion resistance, bullet resistance, UV tolerance, anti-static qualities, and abrasion resistance.
- Infrared transparent with some types transmitting up to 92% of light
Considerations
- Poor impact resistance
- More brittle than ABS
- Often used together with ABS parts to ensure product strength
8. Polyphenylene Ether+Polystyrene (PPE+PS)
Polyphenylene Ester (PPE) and Polystyrene (PS) is a common blend.
PPE+PS has many electrical applications as plastic enclosures for electronics such as relays and housings for transformers.
Attributes
- Great mechanical properties
- Excellent thermal properties, including good resistance to heat distortion
- Great electrical properties
- High resistance to chemicals
Considerations
- Best suited for indoors rather than as an outdoor electronic enclosure
- UV light can cause color distortion
9. Styrene Ethylene Butadiene Styrene (SEBS)
SEBS is a thermoplastic elastomer, which has an elasticity like rubber.
Because it is comfortable to the touch, SEBS is an excellent option for plastic electronic enclosures for handheld cases. It’s also a great alternative to PVC in small plastic toys.
Attributes
- Weather-resistant
- Chemical-resistant
- Pleasant rubber-like feel
Choose the Right Plastic. Choose A&C Plastics
Some attributes to consider when choosing plastic for electrical needs include UV resistance, chemical resistance, temperature tolerance, flame resistance, colorability, transparency, moisture resistance, impact resistance, and stress resistance. A&C Plastics, Inc. has a large variety of plastics for your electronics enclosures. Check out our Electronic Plastics Resource Center for more considerations related to electronic plastics.
Learn More